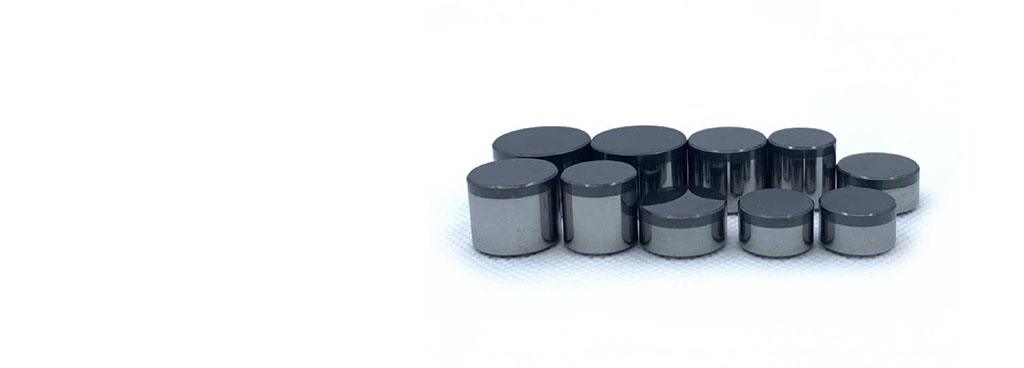
。
# PDC Bit Cutter Technology in Drilling Applications
## Introduction to PDC Bit Cutters
Polycrystalline Diamond Compact (PDC) bit cutters have revolutionized the drilling industry with their superior performance and durability. These cutting tools combine the hardness of diamond with the toughness of tungsten carbide, making them ideal for various drilling applications.
## How PDC Bit Cutters Work
PDC cutters consist of a thin layer of synthetic diamond particles bonded to a tungsten carbide substrate under high pressure and temperature. This unique construction provides:
– Exceptional wear resistance
– High thermal stability
– Superior impact resistance
The diamond table on the cutter’s face provides the cutting action, while the carbide substrate offers structural support and facilitates brazing to the drill bit body.
## Advantages Over Traditional Cutting Tools
Compared to conventional roller cone bits or natural diamond bits, PDC cutters offer several benefits:
### Increased Rate of Penetration (ROP)
PDC bits can drill faster than traditional bits, significantly reducing drilling time and costs.
### Longer Service Life
The extreme hardness of the diamond cutting surface allows PDC bits to maintain sharpness longer than other bit types.
### Reduced Tripping Time
With their extended lifespan, PDC bits require fewer bit changes, minimizing non-productive time.
## Applications in Various Drilling Environments
PDC cutters perform well in multiple drilling scenarios:
### Oil and Gas Drilling
PDC bits dominate the market for soft to medium-hard formations in hydrocarbon exploration.
### Geothermal Drilling
The thermal stability of PDC cutters makes them suitable for high-temperature geothermal applications.
### Mining and Construction
PDC technology is increasingly used in mineral exploration and foundation drilling.
## Recent Technological Advancements
Manufacturers continue to improve PDC cutter technology through:
### Enhanced Diamond Synthesis
New manufacturing processes create more thermally stable diamond tables.
### Innovative Cutter Designs
Asymmetric and shaped cutters improve performance in specific formations.
### Advanced Bonding Techniques
Improved bonding between diamond and substrate increases cutter reliability.
## Challenges and Limitations
While PDC cutters offer numerous advantages, they face some limitations:
– Reduced effectiveness in extremely hard or abrasive formations
– Higher initial cost compared to traditional bits
– Potential for cutter damage in unstable drilling conditions
## Future Outlook
Keyword: pdc bit cutter
The drilling industry continues to invest in PDC technology development, focusing on:
– Improved cutter materials for harder formations
– Smart bits with embedded sensors
– Environmentally friendly manufacturing processes
As these innovations progress, PDC bit cutters will likely expand their dominance in the drilling tool market.