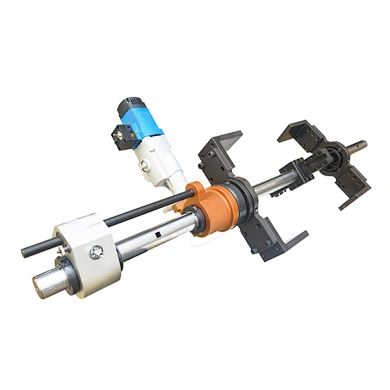
# Flange Preparation Machine for Chemical Plant Maintenance
## The Importance of Flange Preparation in Chemical Plants
Flange preparation is a critical aspect of chemical plant maintenance that ensures safe and efficient operations. Properly prepared flanges create leak-proof connections between pipes, valves, and equipment, preventing hazardous chemical leaks that could lead to environmental contamination, safety hazards, and costly downtime.
## What is a Flange Preparation Machine?
A flange preparation machine is a specialized tool designed to resurface and restore damaged or corroded flanges to their original specifications. These machines typically feature:
– Precision cutting tools
– Adjustable mounting systems
– Automated operation controls
– Safety features for hazardous environments
## Benefits of Using Flange Preparation Machines
### 1. Increased Safety
By restoring flanges to proper specifications, these machines help prevent dangerous leaks of toxic or flammable chemicals.
### 2. Cost Savings
Proper flange maintenance extends equipment life and reduces the need for complete flange replacement.
### 3. Reduced Downtime
On-site flange preparation eliminates the need to remove and transport flanges for off-site machining.
### 4. Improved Seal Performance
Precisely machined flanges ensure better gasket compression and sealing performance.
## Types of Flange Preparation Machines
### Portable Flange Facers
Ideal for field work, these compact machines can be transported to the job site and mounted directly on the flange.
### Stationary Flange Machines
Larger, more powerful machines used in maintenance shops for extensive flange repair work.
### Automated CNC Flange Preparation Systems
Computer-controlled systems for high-precision work on critical flanges in sensitive applications.
## Key Features to Look for in a Flange Preparation Machine
When selecting a machine for chemical plant maintenance, consider:
– Corrosion-resistant materials
– Explosion-proof ratings (for hazardous areas)
– Precision adjustment capabilities
– Compatibility with various flange sizes
– Ease of setup and operation
## Maintenance Best Practices
To ensure optimal performance of your flange preparation machine:
– Regularly inspect cutting tools for wear
– Keep all moving parts properly lubricated
– Store the machine in a clean, dry environment
– Follow manufacturer’s maintenance schedule
– Train operators on proper use and safety procedures
## Conclusion
Investing in quality flange preparation equipment is essential for maintaining the integrity of piping systems in chemical plants. By choosing the right machine and implementing proper maintenance procedures, facilities can significantly improve safety, reduce costs, and minimize operational downtime.